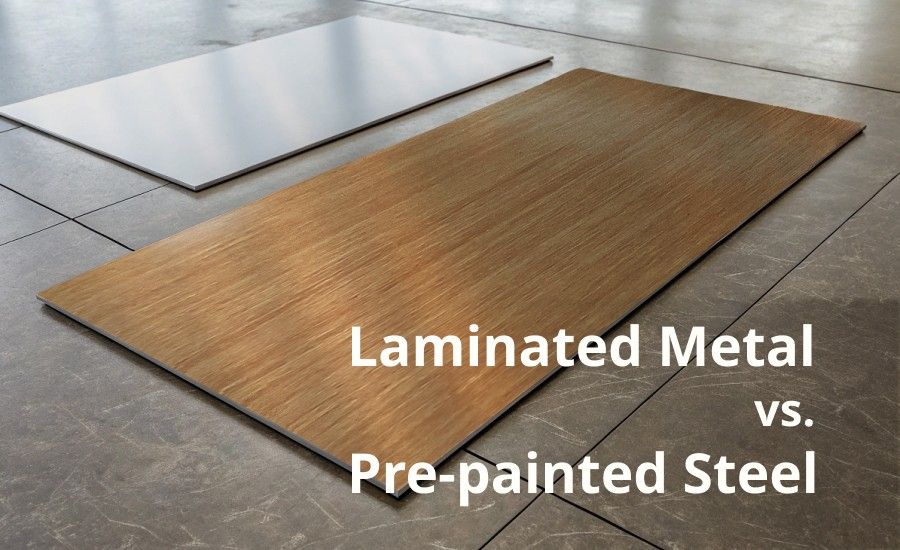
Laminated Metal vs. Pre-Painted Steel: Which Material is Best for Your Application?
When selecting coated steel materials, laminated metal and pre-painted steel are two common choices. Both enhance the appearance and durability of metal sheets by applying a protective coating, but they use different techniques and materials.
Laminated metal utilizes a thin film of PVC, PET, or PP, which is bonded to the metal surface, forming a uniform, thick, and durable protective layer. This provides excellent stain resistance, chemical resistance, and design versatility.
In contrast, pre-painted steel is manufactured by repeatedly applying liquid or powder coatings and then curing them at high temperatures to adhere to the metal surface. While this process offers decorative and protective effects, pre-painted steel coatings are generally thinner, which may lead to reduced corrosion resistance over time. Additionally, the production process of pre-painted steel may generate higher VOC (volatile organic compound) emissions, posing environmental concerns.
Overall, laminated metal offers better formability, lower maintenance costs, and wider applications in home appliances, construction, interior design, and industrial equipment.
It is especially suitable for environments requiring stain resistance, weather resistance, or high-end aesthetics.
Laminated Metal vs. Pre-Painted Steel: Performance Comparison
Comparison Criteria | Laminated Metal (PVC, PET, PP) | Pre-Painted Steel |
---|---|---|
Thickness & Surface Protection | Thicker laminated layer (100–200µm)prevents surface damage and effectively resists moisture. | Thickness varies (10–150µm). Except for powder coatings, most are relatively thin and prone to scratches or wear. |
High-Temperature Resistance | Depends on the film type—PET and PP offer better heat resistance, while PVC is suited for ambient temperatures. | Can withstand high temperatures, but some coatings may discolor or degrade under prolonged heat exposure. |
Aesthetic Options | Offers a variety of textures and colors (e.g., wood grain, leather, stone, metallic finishes) in glossy or matte options. | Primarily available in solid colors, with limited special texture designs. |
Formability & Processing | Highly flexible; resistant to cracks or peeling during bending, stamping, or stretching. | Coating may develop fine cracks or wear off under deep drawing or bending, affecting longevity. |
Quality Stability | Advanced lamination technology ensuresuniform thickness and consistent quality. | Coating thickness may be uneven due to the painting process, affecting quality. |
Stain & Chemical Resistance | Highly resistant to stains and oil adhesion, effectively prevents acid and alkali corrosion—ideal for humid or chemical environments. | Exposure to acids, alkalis, or strong cleaners may cause discoloration or brittleness. Requires special painting or additional protective coatings; prolonged exposure to moisture may lead to rust. |
Environmental Impact | Requires only film bonding to metal, resulting in low VOC emissions—more environmentally friendly. | Involves multiple coating applications and high-temperature curing, generating higher VOC emissions. |
Cost & Long-Term Benefits | Higher initial material cost, but superior durability reduces maintenance, rework, and replacement expenses. | Lower initial cost but more susceptible to damage, leading to higher maintenance frequency. |
Applications | Suitable for buildings, home appliances, furniture, cleanrooms, medical equipment, and industrial uses. | Primarily used for roofs, exterior walls, doors, windows, and sheet metal parts. |
If your application requires greater design flexibility and enhanced formability, laminated metal is the ideal choice.
Compared to pre-painted steel, the thicker and more uniform protective layer of laminated metal offers a wider variety of textures and colors while maintaining surface integrity during bending and forming.
It is also produced using advanced lamination techniques that ensure consistent quality and lower VOC emissions, making it a more environmentally friendly option.
While the initial material cost is higher, its durability and superior protection lead to reduced maintenance and replacement costs, making it a cost-effective solution in the long run.
For further information, check out these resources: